The Challenge
The construction of a natural gas compression plant in northwest Mexico has presented unique challenges in pipe support systems. Traditional methods failed to deliver the desired results due to temperature fluctuations and substrate compatibility issues. The trusted distributor for UNIQUE POLYMER SYSTEMS in Mexico, proposed an innovative solution using UPS 365 RR RUBBER REPAIR 60 cold vulcanizing product to ensure optimal adhesion of neoprene plates to pipe supports.
During the plant's construction, the contractor faced difficulties in adhering neoprene plates to various pipe supports, some of which required bonding around the pipe circumference. The initial use of epoxy-based glue, despite mechanical cleaning, proved ineffective due to temperature changes (from 5°C in winter to 50°C in summer) and lack of elongation and compatibility with substrates, leading to peeling issues.
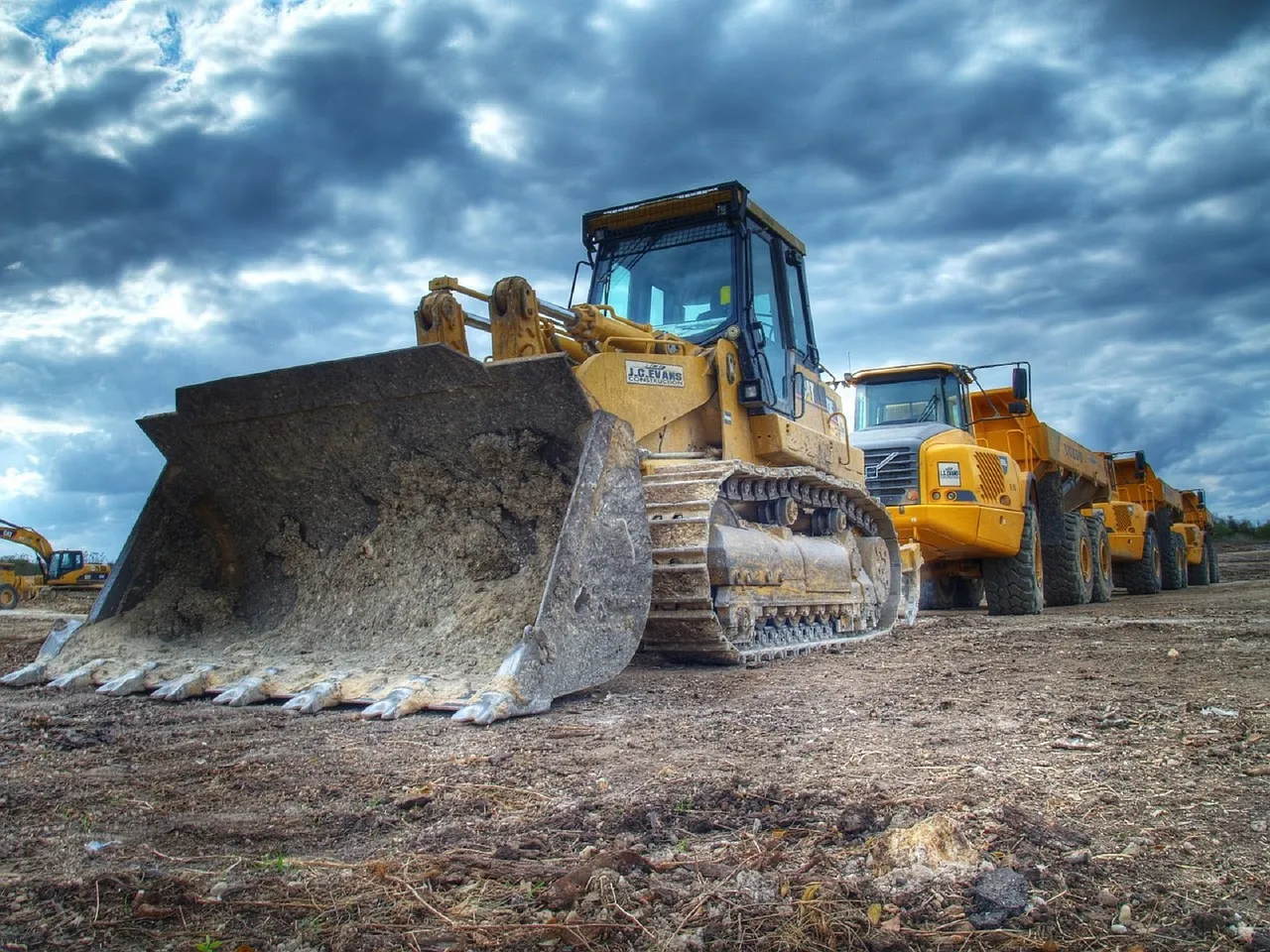